Government relations: Working for the sector
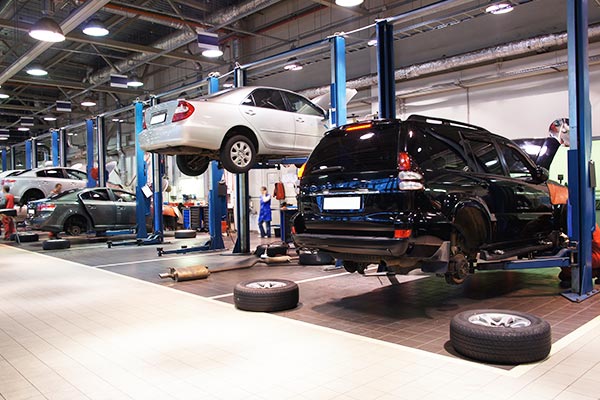
Issue 1: Right to Repair
Modern, web-connected vehicles collect thousands of data points on the health of vehicle systems. Without access to this data, independent auto repair shops cannot service a vehicle.
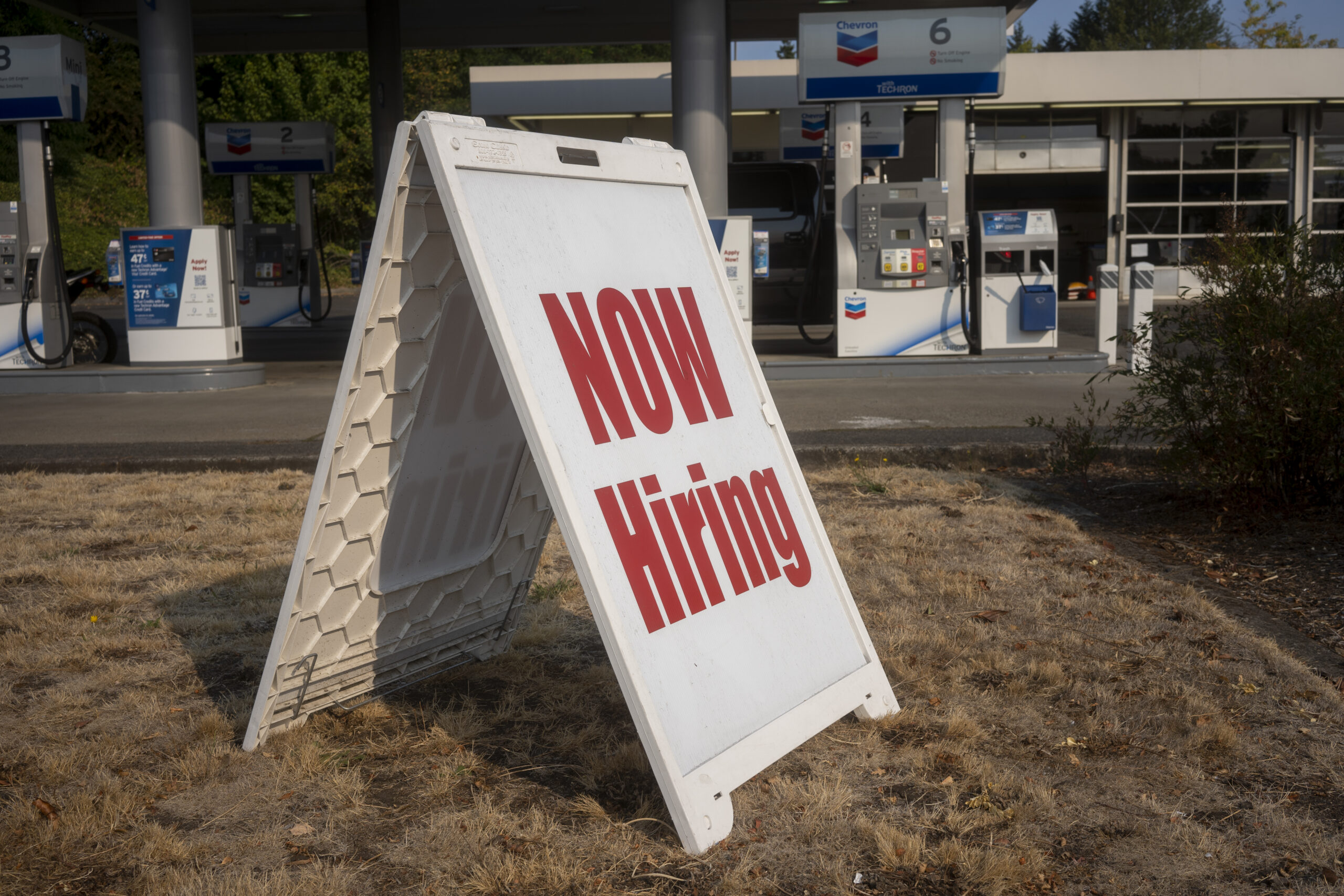
Issue 2: Labour
The auto care sector is facing a skills shortage caused by rising retirement rates and a decrease in registrations for apprenticeship programs. Find out more about how we’re helping address this issue.
About the auto care sector
AIA Canada represents, supports and leads innovation in Canada’s $43.9 billion auto care sector.
With more than thousands of members from coast to coast, our vision, research, training programs and advocacy supports Canada’s collision and mechanical sectors.
Our best practices for the auto care industry help our members keep Canada’s fleet of almost 26.6 million vehicles on the road.
Government relations matters
Politics impacts every part of your business. At the same time, political decision-makers often don’t fully grasp exactly how their choices or inaction will impact you, your business and your employees.
Decision-makers can’t fix problems they don’t know about, which is why they need to be engaged directly by those affected.
The Government Relations team at AIA Canada is working for our members and sector overall to advance issues and concerns that will impact the future of the sector. We are focused on what matters to our membership and take a targeted approach to raise our concerns with key decision makers who can then take action.
Transportation of dangerous goods
Equivalency Certificates, issued by Transport Canada, authorize AIA Canada’s members to transport various dangerous goods.
AIA Canada members can access for download the Equivalency Certificate here by login into their member account.
Members can access online health and safety training via the Bistrainer website.
For inquiries related to the transportation of dangerous goods, please email our Government Relations team at gr@aiacanada.com.
Latest news
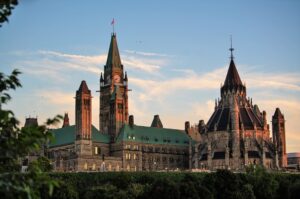
Why the right to repair needs to be a priority in the new government
To state that Canadians have had an economically tumultuous start to 2025 would be an understatement. That is particularly the case for the auto care
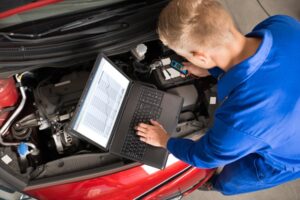
Vehicle data ownership and the right to repair: Insights from Canadian consumers
For most Canadians, the concept of the right to repair sounds like common sense. If you own a vehicle, you should be able to choose
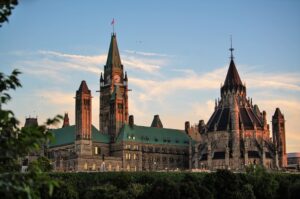
New Cabinet announced: Key opportunities for AIA Canada’s advocacy
Today, the Rt. Hon. Mark Carney, Prime Minister of Canada announced his cabinet, the body of ministerial advisors that sets the federal government’s policies and
Our team
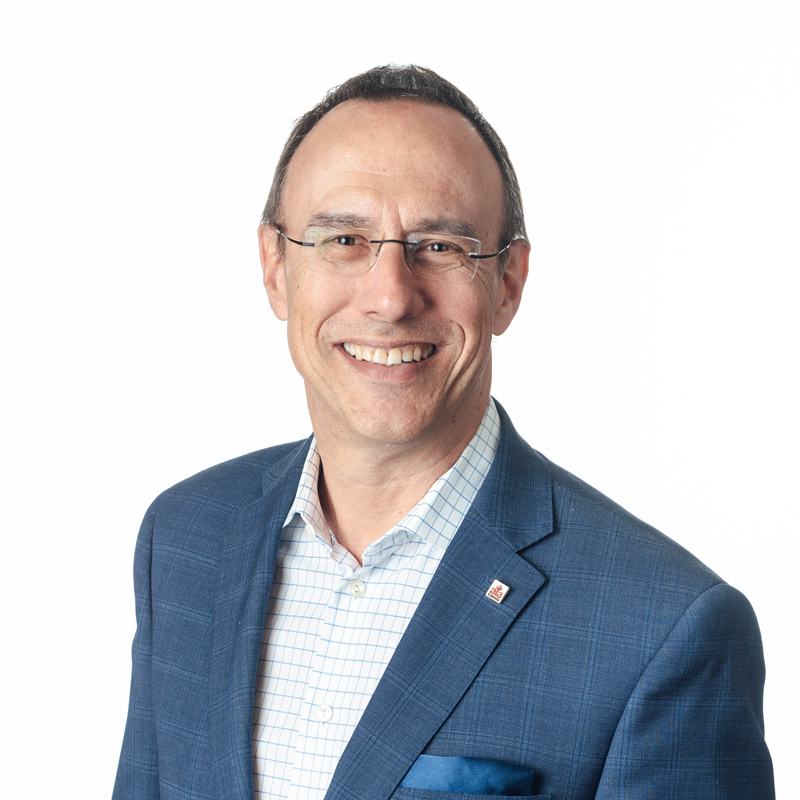
Jean-François Champage, CAE
Jean-François (JF) Champagne is the president and chief executive officer of the Automotive Industries Association of Canada (AIA Canada), a non-profit organization that is the voice and resource of a $43.9 billion industry with thousands of professional members from coast to coast. Under JF’s leadership, AIA Canada brings together the entire auto care supply and service chain and equips its members with the tools, skills, profile, and knowledge they need to succeed in a fast-paced, competitive landscape.
Since joining AIA Canada in 2015, JF has focused his efforts on helping guide members and the sector overall on a variety of issues, including electric vehicles (EV), labour sustainability and digital transformation.
As a Certified Association Executive (CAE) and a technology visionary, JF leads with a focus on ensuring organizations thrive in the digital age. He is a regular speaker at automotive industry and association-management conferences, where he shares his expertise on the integration of technology in strategic planning to help shape better and stronger organizations.
JF Champagne currently serves as the Chair of the Canadian Automobile Service Information Standard (CASIS), as the Vice-Chair of the Canadian Society of Association Executives (CSAE) and as a board member of the Automotive Business School of Canada (ASBC). He is also a representative on the Canadian Automobile Partnership Council (CAPC).
Interested in getting involved?
For more information or to discuss other ways you can get involved, please contact our Government Relations team.